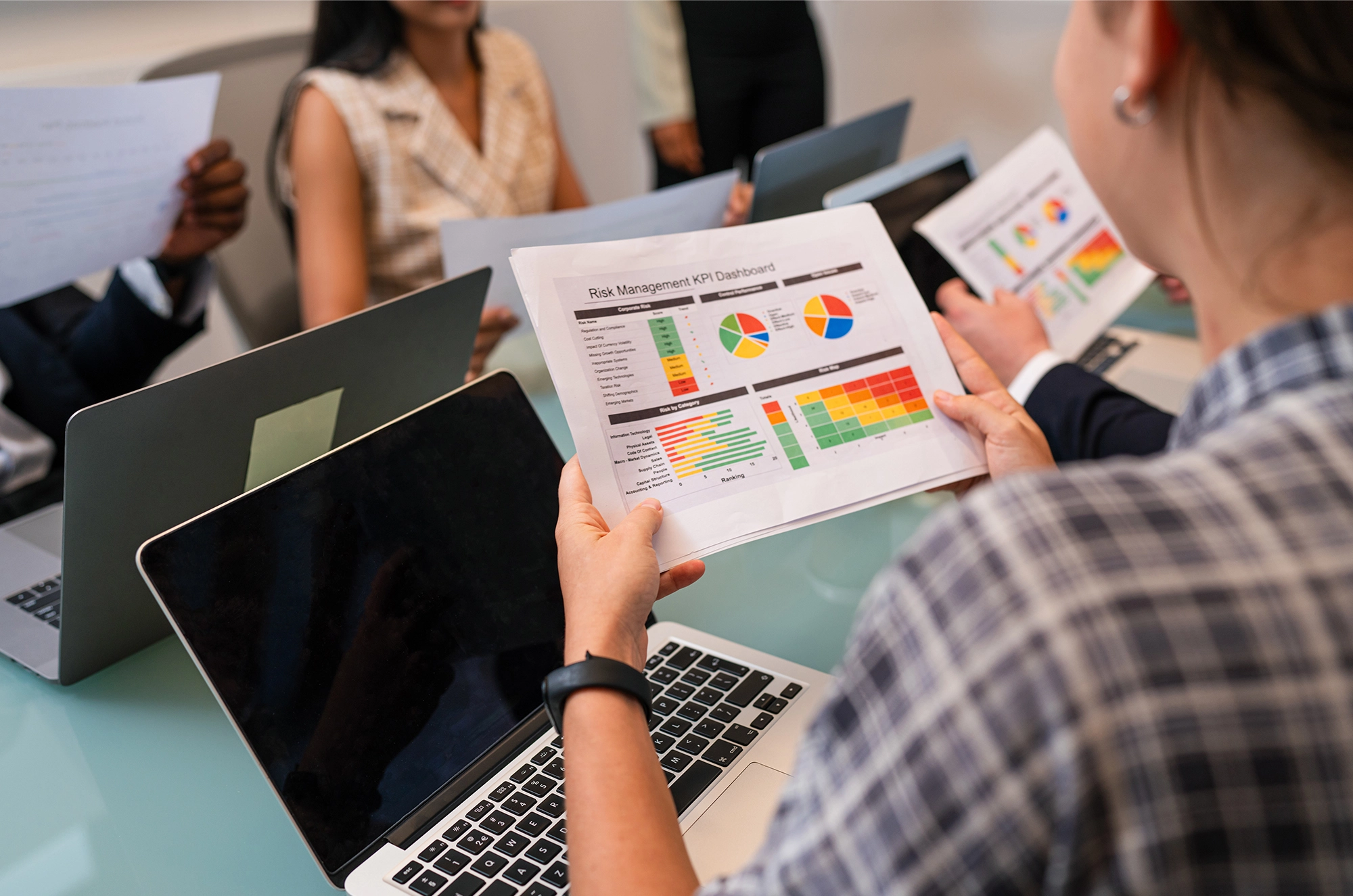
Analyzing Core Business Process Cycles
Analyzing core business process cycles is essential for improving efficiency, enhancing performance, and driving business success. By understanding and optimizing these cycles, businesses can streamline operations, reduce costs, and achieve better outcomes. Here’s how to analyze core business process cycles effectively:
-
Identify Core Processes: Begin by identifying the core processes that are critical to your business operations. These may include sales, marketing, production, supply chain management, customer service, and finance. Understanding the key processes helps in focusing analysis efforts on the most impactful areas.
-
Map Process Workflows: Create detailed process maps that outline the steps, activities, and stakeholders involved in each core process. Process mapping provides a visual representation of workflows, highlighting the sequence of tasks and interactions. This helps in identifying bottlenecks, redundancies, and areas for improvement.
-
Collect Process Data: Gather data on the performance of core processes, including metrics such as cycle time, throughput, error rates, and resource utilization. Data collection can be done through process monitoring, employee feedback, and performance reports. Accurate data is essential for meaningful analysis.
-
Analyze Process Performance: Use data analysis techniques to evaluate the performance of core processes. Identify trends, patterns, and variations in process metrics. Analyzing performance data helps in understanding the effectiveness and efficiency of processes.
-
Identify Bottlenecks and Inefficiencies: Look for bottlenecks, delays, and inefficiencies in process workflows. Bottlenecks are points where processes slow down or get stuck, affecting overall performance. Identifying and addressing these issues is crucial for optimizing process cycles.
-
Evaluate Process Interdependencies: Understand the interdependencies between different processes and how they impact each other. Analyzing process interdependencies helps in identifying potential risks, coordinating activities, and ensuring smooth transitions between processes.
-
Benchmark Against Best Practices: Compare your process performance with industry benchmarks and best practices. Benchmarking provides insights into how your processes stack up against competitors and identifies opportunities for improvement. Adopting best practices can lead to significant performance gains.
-
Implement Process Improvements: Based on the analysis, develop and implement process improvement initiatives. This may involve re-engineering workflows, adopting new technologies, automating repetitive tasks, and enhancing employee training. Continuous improvement ensures that processes remain efficient and effective.
-
Monitor and Measure Impact: Regularly monitor the impact of process improvements on performance metrics. Use key performance indicators (KPIs) to track progress and evaluate the effectiveness of changes. Continuous monitoring helps in sustaining improvements and making further adjustments as needed.
-
Engage Stakeholders: Involve stakeholders, including employees, managers, and customers, in the analysis and improvement of core processes. Stakeholder engagement provides diverse perspectives, fosters collaboration, and ensures that improvements are aligned with business goals.
-
Leverage Technology: Utilize technology and automation tools to enhance process efficiency. Business process management (BPM) software, workflow automation tools, and data analytics platforms can streamline operations and provide real-time insights into process performance.
-
Ensure Compliance and Quality: Ensure that core processes comply with regulatory requirements and quality standards. Regular audits and quality checks help in maintaining compliance and delivering consistent, high-quality outcomes.
-
Document Processes: Maintain detailed documentation of process workflows, performance metrics, and improvement initiatives. Documenting processes provides a reference for training, audits, and future analysis. It also helps in preserving institutional knowledge.
-
Promote a Culture of Continuous Improvement: Foster a culture of continuous improvement within the organization. Encourage employees to identify and suggest process improvements, and recognize their contributions. A culture of continuous improvement drives innovation and enhances overall performance.
-
Align with Strategic Goals: Ensure that process improvements align with the overall strategic goals of the business. Process optimization should support key objectives such as growth, customer satisfaction, and operational excellence. Alignment with strategic goals ensures that efforts are focused on achieving desired outcomes.
By analyzing and optimizing core business process cycles, businesses can improve efficiency, reduce costs, and achieve better performance. A systematic approach to process analysis and improvement drives sustainable growth and enhances overall competitiveness.